Comparison of Dyeing and Bleaching Processes
Dyeing processes
In textile production, fibers, yarns or the finished sewn product are refined by dyeing. There are various dyeing processes, the application of which depends on the type of fibers and the properties of the dye used. Textile dyeing is expected to be as colour fast as possible.
Colour fastness means the behavior of dyed textiles under certain environmental and everyday conditions. The dye used should not come off the fiber during the first wash or as a result of friction. Accordingly, the dye must be firmly anchored to the fiber.
Three dyeing processes can be distinguished:
Direct dyeing: untreated fabric is dipped into a solution of the dye
Development dyeing: dye is first formed on the fiber
Disperse dyeing: dye is dissolved in the fiber
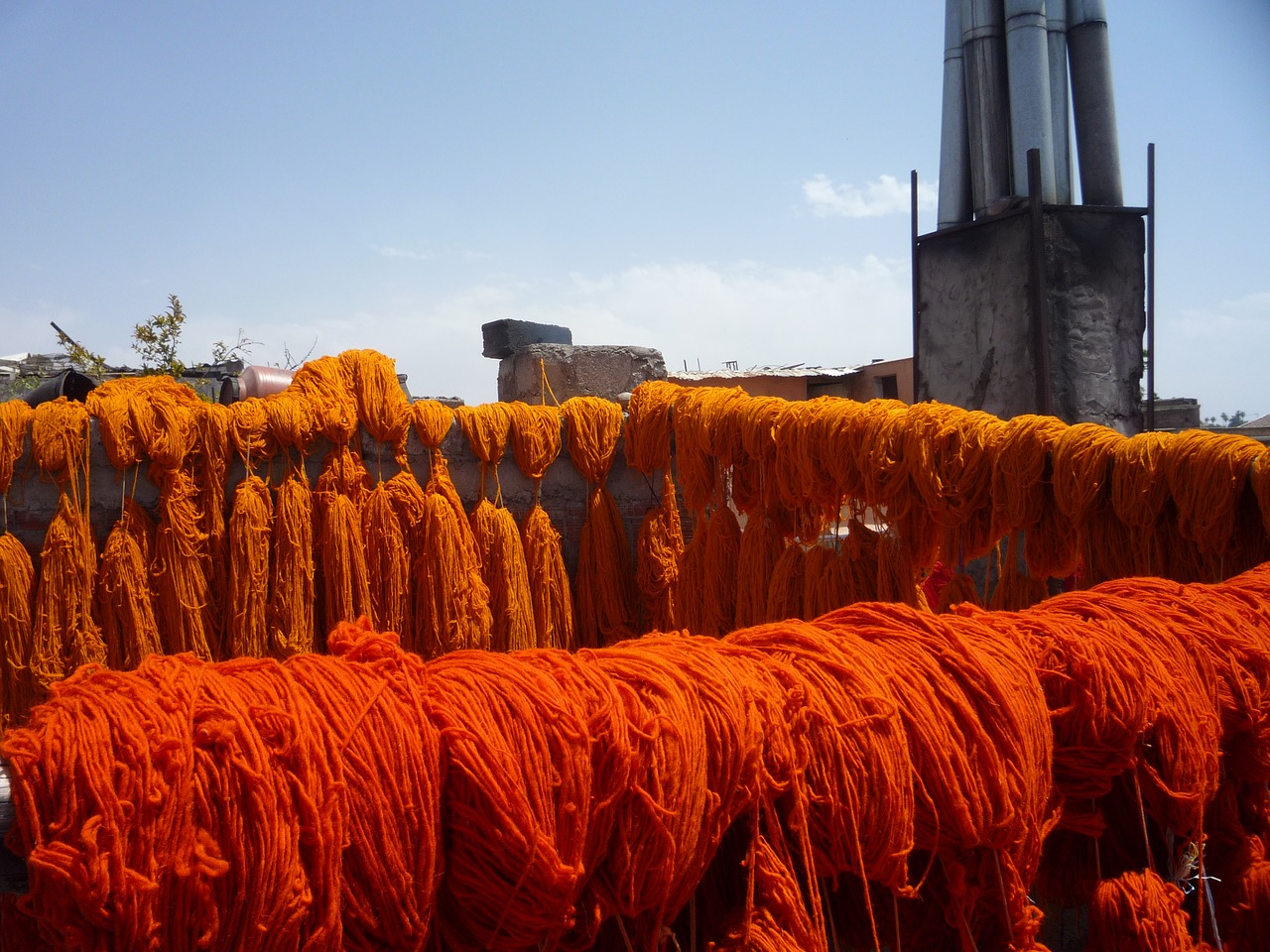
1. Direct dyeing
When the dye is applied directly to the fiber, it is called direct dyeing. Pre-treatment of the fibers is not necessary in this process. The fibers directly draw the water-soluble dye from the pH-neutral dye bath. It diffuses into the fibers and anchors itself there. Depending on the anchoring, a distinction is made between two types:
In substantial direct dyeing, the dye adheres to the fibers through van der Waals interactions and hydrogen bonds. These anchors are usually not very strong, which is why fabrics dyed by this method are not washfast. Substantial dyes are mainly azo dyes. This type of dyeing is used for cotton and other cellulosic fibers.
In ionic direct dyeing, the dye molecules, such as crystal violet, carry a positive or negative charge. These dyes form an ionic bond with the oppositely charged atomic groups of the fibers. Especially protein-containing fibers such as wool or silk can be dyed well with this method. Acidic dye molecules, which form anions by releasing protons, are particularly suitable for this purpose. This is why they are called anionic dyes. The resulting ionic bonds are stronger than the intermolecular forces in substantial direct dyeing and make the dyed textiles more resistant to washing.
2. Development dyeing
In contrast to direct dyeing, in development dyeing the dyes are formed directly on the fiber. A distinction is made between vat dyeing, mordant dyeing and reactive dyeing.
The dye in vat dyeing is insoluble in water and thus has a higher wash fastness. However, they cannot be applied directly to the fibers. They are therefore first converted into a water-soluble form by means of a reducing agent. Since the reduced form is usually no longer coloured, it is called leucoform (Greek leukos = white). As with direct dyeing, the solution can now be further processed.
While the dyeing material dries, the leucoform of the dye oxidizes and regains its colour. The process can be accelerated with oxidizing agents. Indigo is one of the most important vat dyes. Even though these have a higher washfastness, indigo-dyed fabrics fade over time. The dye adheres to the fiber due to van der Waals interactions and hydrogen bonds, and detaches from it when subjected to mechanical stress.
Due to the high heavy metal contamination of the fibers and the waters, mordant dyeing is hardly used today. In this process, the fibers are pre-treated with metal-containing salts before dyeing. Aluminum and iron salts in particular are used. The metal salts become embedded in the fibers and form stable complex compounds with the dye molecules. Mordant dyeing is mainly used for wool, because the dye adheres particularly well to the fibers due to the chemical structure of wool and results in a very high wash fastness.
In reactive dyeing, the dye has a reactive group that has nothing to do with the colour itself. This is able to form an atomic bond with the hydroxy groups of cellulose fibers. It reacts with the cellulose fiber by splitting off a chlorine atom. The dye is thus particularly firmly anchored to the fiber, resulting in a very durable dyeing with very high wash fastness.
3. Disperse dyeing
Dispersion dyeing is used for non-polar fibers, such as polyester fibers. The water-insoluble dyes, mostly azo dyes, are processed with auxiliaries to form a suspension. The colorant is finely dispersed in this suspension. The fibers are "expanded" by temperature and other auxiliaries. The colorant diffuses into the fibers, resulting in a very washfast and lightfast dyeing.
Bleaching processes
Bleaching is a textile chemical process in which existing dyeing on natural fibers is removed and the degree of whiteness is increased. This is done with an oxidative or reductive bleaching agent.
For cotton and other cellulosic fibers, bleaching is commonly used to prepare the fiber structure before actual dyeing. For modern synthetic fibers, the process is not necessary. Here, attention is already paid to an appropriate degree of whiteness during the production of the fibers.
The bleaching process is usually carried out with hydrogen peroxide, caustic soda and surfactants as well as other chemical auxiliaries such as bleach stabilizers. Depending on whether vegetable (cellulose e.g. cotton) or animal fibers (proteins e.g. sheep's wool) are to be bleached, the pH value varies. Cotton, for example, is bleached alkaline, while sheep's wool is bleached in the acidic range. In this process, the chemical components react with each other. Due to the bleach stabilizer, the oxygen is slowly split off from the hydrogen peroxide in a controlled manner. Uncontrolled, spontaneous decomposition would reduce the length of the molecular chains of the cellulose, resulting in reduced tensile strength.
Bleaching has several objectives:
Decolourization through the oxidation of the basic dye
Removal of plant impurities (leaf residues and the like from harvest)
Removal of fats
Absorbency for subsequent processes is increased and made more uniform
Two bleaching processes are distinguished: continuous bleaching and discontinuous bleaching.
1. Continuous bleaching
In this process, a mixture of hydrogen peroxide, caustic soda, stabilizers and water (called bleaching liquor) is applied to the textile fabric. Then the decomposition of the hydrogen peroxide is activated in a continuous steamer at a temperature of about 100°C. The process takes little time but has high energy costs.
2. Discontinuous bleaching process
In this process, the bleaching liquor is applied to the fabric, which is left to rotate on large rolls (bails or docks) for up to 24 hours. Since no process heat is required as in the continuous bleaching process, the energy costs are low.
Another such process is the bleaching of yarn on bobbins or warp beams. The process is carried out in large boilers under pressure and at high temperatures in the bleaching liquor.
Depending on the process, the individual components are added to the bleaching liquor in different mixing ratios. The fabric must be washed after bleaching so that subsequent processes, e.g. in the print shop or during dyeing, are not disturbed. That is because remaining hydrogen peroxide can destroy the dyes.
Sources:
Bleichen von Hans-Peter Willig (Bleaching by Hans-Peter Willig)
Bleichen von Lumitos GmbH (Bleaching by Lumitos GmbH)
Chemie am Menschen – Färbeverfahren von Chemiezauber.de (Chemistry on Humans - Staining Processes by Chemiezauber.de)
Färbeverfahren von Bibliographisches Institut GmbH (Dyeing processes by Bibliographisches Institut GmbH)
Textilindustrie von Umweltbundesamt (Textile industry by the Federal Environment Agency Germany)
Picture from Pixabay